Alta tensione: aumentare il voltaggio dei sistemi elettrici per ottimizzare l’efficienza dei veicoli
L’elettrificazione, trend tecnologico ormai imperante nel settore dei veicoli commerciali, porterà a un ripensamento di tutta la parte elettrica, meccatronica ed elettromeccanica. Con implicazioni significative in termini di efficienza, sicurezza e possibile riduzione dei costi. Ne abbiamo parlato con Marcello Nizzoli, Business Development Director di General Cab Group.
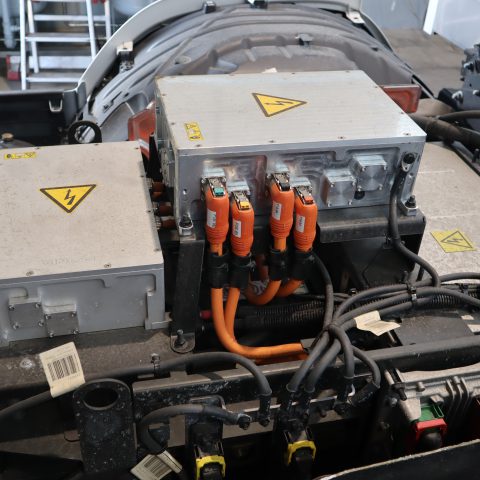
L’elettrificazione, trend tecnologico ormai imperante nel settore dei veicoli commerciali, porterà a un ripensamento generale non soltanto dei componenti più intrinsecamente legati alla trazione dei veicoli, ma anche di tutta la parte elettrica, meccatronica ed elettromeccanica. Una diversa concezione ingegneristica che, secondo Marcello Nizzoli*, attualmente Business Development Director di General Cab Group con esperienza più che ventennale nel marketing strategico del settore automotive, porta in dote molte opportunità per i costruttori di componentistica, soprattutto, se le case costruttrici dei veicoli, saranno disposte a rivedere i consueti impianti elettrici a basso voltaggio, a 12 e 24 Volt, a favore di un più funzionale ed efficiente alto voltaggio.
“Per decenni – spiega Nizzoli – i voltaggi si sono stabilizzati sui 12V o 24V, con pochissime eccezioni per il settore dei carrelli elevatori, per esempio. Anche in agricoltura, piuttosto inspiegabilmente, fatta eccezione per alcuni grandi macchinari, siamo generalmente ancorati ai 12V. Il voltaggio a 48V, timidamente citato già all’inizio degli anni Duemila in quasi tutte le presentazioni delle capacità industriali di fornitura, sta ancora avanzando piuttosto lentamente e solo nella nicchia dei veicoli mild-hybrid. Questa lenta introduzione, a mio parere, è inspiegabile, visto che su autobus e camion, l’introduzione della tecnologia a 48V potrebbe comportare una riduzione dei pesi, nonché dei costi, di tutti i componenti elettrici, compresi i cablaggi. Con l’effetto di una maggiore efficienza generale di funzionamento ed economica del veicolo”.
Il voltaggio dei sistemi elettrici nei veicoli commerciali
La necessità di progettare veicoli commerciali elettrici, oggi, può cambiare lo scenario appena descritto?
“I veicoli elettrici hanno rappresentato sicuramente una svolta anche per i produttori di componentistica elettrica e meccatronica. Le batterie e i motori elettrici per la trazione, per varie ragioni, sono ormai standardizzati tra i 300V e gli 850V, con una netta tendenza alle tensioni più alte, per ragioni tecniche, di efficienza, autonomia, rapidità di ricarica e costi della gestione termica generale, nonché per le dimensioni più ridotte di cavi e cablaggio. Ci sono già offerte di compressori di gas per applicazioni di thermal management ed HVAC (riscaldamento, ventilazione, condizionamento dell’aria, ndr) alla tensione di 850V. Il cambiamento, però, potrebbe essere più netto…”.
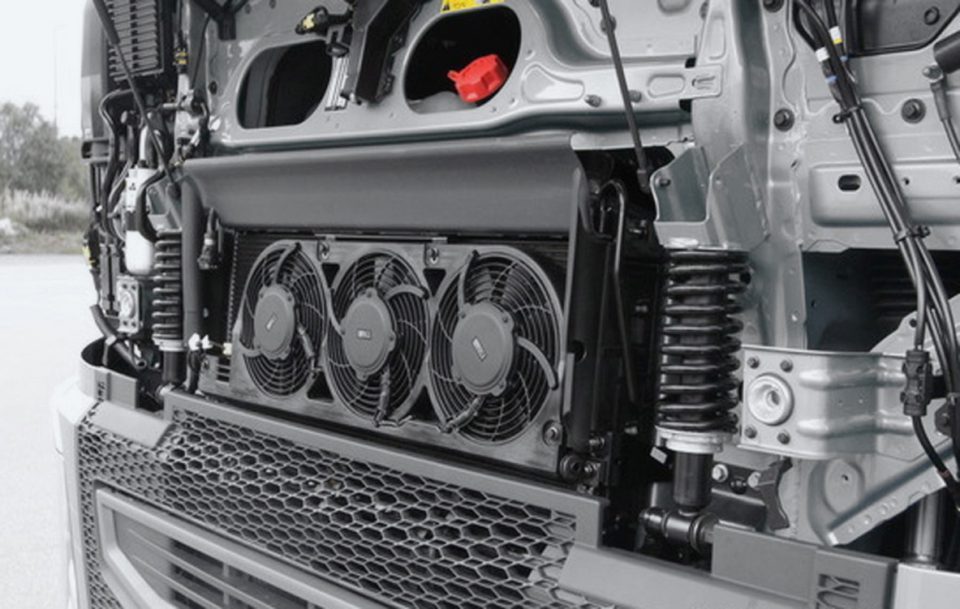
In che senso?
“Se allarghiamo lo sguardo alla totalità di un veicolo, vediamo che molti altri componenti potrebbero essere elettrificati ad alta tensione. Mi riferisco soprattutto al thermal management delle batterie, oggi caratterizzato ancora da alti consumi energetici, con l’effetto di ridurre notevolmente l’autonomia di guida del mezzo. Su questo tipo di componenti siamo ancora su standard da 12V o 24V”.
Per quale motivo, dal suo punto vista?
“Il mercato dei veicoli elettrici oggi è ancora caratterizzato da volumi produttivi piuttosto bassi: basta guardare gli ultimi dati di vendita delle stesse auto elettriche, per non parlare di veicoli per certi versi più complessi come i commerciali e gli industriali. La filiera delle forniture automotive, insomma, si trova ad un bivio: da un lato, i costruttori chiedono insistentemente voltaggi alti perché implicano benefici tecnici, economici, di riduzione del numero di componenti, anche a vantaggio dell’efficienza generale del veicolo. Dall’altro lato, la filiera automotive ‘tradizionale’, quella europea, sta valutando se iniziare seriamente la produzione dei componenti a 300V – 850V o simili – ad alta tensione, insomma. Oggi questi componenti ad alta tensione generano ancora una domanda piuttosto limitata e presuppongono, al tempo stesso, standard tecnici obbligatori, specifiche di progetto non ancora ben delineati dagli stessi costruttori dei veicoli”.
La questione della sicurezza
C’è, a questo proposito, una questione più strettamente legata alla sicurezza dei sistemi e dei loro componenti ad alto voltaggio? E come la stanno affrontando i costruttori?
“Quando si parla di sistemi fino a 48V, si parla, anche a livello normativo di “bassissima tensione”, BBT. Superando la soglia dei 120V, fino a 1.500V, in corrente continua, anche le normative cambiano decisamente, pur definendola ‘bassa tensione’, BT, affrontano problemi molto seri, anche per la sicurezza delle persone che devono operare sul veicolo e sui suoi componenti, contraddistinti, chiaramente, dal colore arancione, affrontando concreti pericoli di possibili folgorazioni, se vanno in contatto con parti in tensione. Questo cambio di voltaggio fa sì che le tradizionali fabbriche di componentistica automotive a 12V, 24V, ma anche 48V, siano profondamente diverse, per le protezioni agli operatori, rispetto a quelle che producono materiale ad oltre 120V di tensione, anche solo per il collaudo finale, quindi per la necessità di confinamento di aree della fabbrica potenzialmente pericolose per le persone”.
Si è parlato di un’industria automotive, quella europea, soprattutto, che sta cercando faticosamente di cambiare pelle, con l’avvento della mobilità elettrica, per resistere alla crescita – anche in termini di competenze – di altre realtà, come quelle del Far East, per esempio. Su quale terreno si giocherà la competizione nel prossimo futuro?
“La sfida europea all’elettrificazione della mobilità non passa solo dalla ‘punta dell’iceberg’ delle batterie al litio e dalle loro materie prime, rare, correlate – oggi, soprattutto controllate dalla Cina – ma anche da eventuali nuove opportunità per la filiera industriale della componentistica automotive, soprattutto italiana, che potrebbe crearsi un vantaggio competitivo, grazie alle sue proverbiali reattività e flessibilità produttive. Questa opportunità, però, potrà concretizzarsi solo se le industrie sapranno prendere decisioni velocemente e nella direzione giusta, evitando errori strategici od eccessivi temporeggiamenti”.
Cioè?
“Dovremo sempre più pesare le reali opportunità e relative decisioni attraverso attenti studi di marketing strategico di prodotto, con la giusta intelligence industriale, per conoscere meglio la transizione elettrica e tutte le relative coniugazioni tecniche ed applicative. Le considerazioni appena fatte, valgono sia per i veicoli full-electric, i cosiddetti BEV, sia per quelli a celle a combustibile alimentate ad idrogeno, FCEV, meno efficienti e che necessitano di sistemi tecnici più sofisticati e dispendiosi d’energia elettrica, anche richiesti dalla pericolosità del gas utilizzato”.
Non solo veicoli elettrici: motore termico e consumi
È giusto che la lente d’ingrandimento tecnologica sia puntata sui veicoli a trazione alternativa ma, l’abbiamo detto, attualmente i volumi importanti sono ancora generati dai veicoli con motore termico, che per i mezzi commerciali significa sostanzialmente con propulsione diesel. Parlando di ventilazione e raffreddamento, ci sono dei modi per incrementare l’efficienza anche nei powertrain tradizionali?
“Certamente sì: parliamo non solo d’efficienza, ma anche di riduzione di consumi, di emissioni inquinanti e climalteranti. Costruttori come Volvo, per fare un esempio, hanno già introdotto sui bus L13 la ventilazione elettrica dell’intercooler e del liquido di raffreddamento motore, in modo da ridurre al minimo le inefficienze e le rigidità della tradizionale ventilazione meccanica o con costosi e complicati motori oleodinamici. Questa innovazione, apparentemente semplice, è partita in UK qualche anno fa, grazie alla pressione della London Transport Autority che ha obbligato i costruttori locali di bus, cioè dei celebri double deckers rossi, come Alexander Dennis Ltd., all’elettrificazione del raffreddamento dei veicoli diesel, altrimenti vietati nell’area metropolitana della capitale del Regno Unito, soprattutto, per motivi di rumore, ma anche per la conseguente riduzione delle emissioni di gas. Inoltre, le tradizionali ventole meccaniche o a trascinamento oleodinamico, oltre che molto rumorose, hanno assorbimenti, spesso, non correlati alla necessità di raffreddamento del veicolo, perché rigidamente connesse al regime di rotazione del motore diesel, quindi, a volte, ventilano, in eccesso, il radiatore, a basse temperature e non abbastanza quando questo raggiunge limiti critici, costringendo, i tecnici, ad inefficienti sovradimensionamenti delle prestazioni di raffreddamento”.
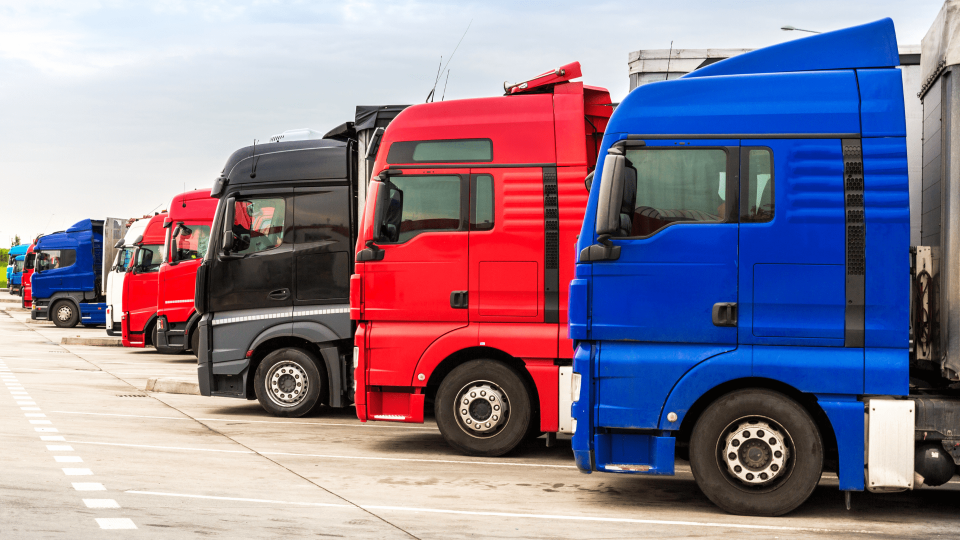
E sui camion?
“Che io sappia non è stata ancora introdotta la ventilazione elettrica dei radiatori dei camion, che invece sta prendendo piede su van e furgoni di taglia media. Sui grandi camion, destinati alla logistica di lungo raggio, da anni, sono state, invece, introdotte delle climatizzazioni alternative ausiliarie elettriche, della cabina, i cosiddetti parking coolers, che funzionano quando il motore diesel deve essere spento, in sosta, per non inquinare e non far rumore. Questi avanzati sistemi elettrici di climatizzazione garantiscono il comfort all’interno della cabina, per il riposo del conducente, anche in piena estate, per varie ore. General Cab Group sin dall’introduzione di questa innovazione tecnologica, per ridurre l’impatto ambientale dei grandi camion, si è specializzata nello sviluppo e produzione di elettroventilatori intelligenti, grazie all’integrazione con l’elettronica, destinati proprio ai parking coolers, sia quelli integrati, OEM che quelli aftermarket, sia da tetto che montati nella parte posteriore della cabina. Anche l’applicazione di elettropompe per la circolazione del liquido di raffreddamento, oltre ai turbocompressori elettro-attuati e ai compressori elettrici per l’aria condizionata potrebbero rappresentare spacchettamenti dei servizi oggi calettati ai motori endotermici diesel tradizionali, per i camion. Questi spacchettamenti hanno lo scopo di ridurre la quantità d’energia meccanica che deve fornire il motore diesel al veicolo, per il suo funzionamento generale e quindi contribuire al miglioramento dell’efficienza, alla riduzione delle emissioni, sia inquinanti che climalteranti. Lo spacchettamento ha, come secondo risultato, quello di un miglioramento delle funzionalità fornite dai nuovi, singoli componenti elettrici, meccatronici, che operano indipendentemente dal regime di rotazione del motore diesel”.
* Marcello Nizzoli è Business Development Director di General Cab Group. Un professionista con oltre 22 anni di esperienza nel marketing strategico del settore automotive OEM, sempre più specializzato nei veicoli sostenibili, elettrici, autobus, camion, mezzi commerciali per la logistica. Dal 1987 studia a livello universitario l’economia e la politica della mobilità.