Lì dove nascono le batterie per veicoli industriali. Il nostro viaggio nella Gigafactory indipendente più grande d’Europa
BorgWarner ci ha aperto le porte della sua Gigafactory di Darmstadt, in Germania, in grado di produrre circa 35.000 pacchi batterie Nmc in un anno grazie a linee innovative e altamente automatizzate. Previsti investimenti sulle batterie Lfp per ampliare il portfolio.
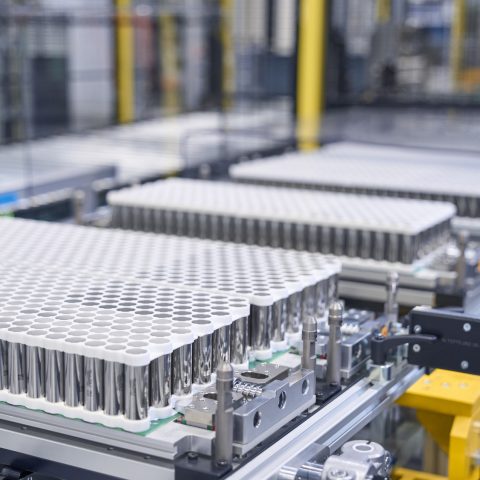
Prima del Covid, quindi fino a pochi anni fa, non c’era nulla. Adesso, a Darmstadt, c’è una delle Gigafactory più attrezzate d’Europa. La più grande se si escludono quelle che appartengono agli Oem. L’acquisizione, perfezionata nel 2022, ha dato a BorgWarner accesso all’impianto per la produzione di batterie di Akasol. Un impianto che oggi lavora su tre turni cinque giorni alla settimana (sono stati anche sette, in passato) utilizzando linee produttive all’avanguardia e altamente automatizzate.
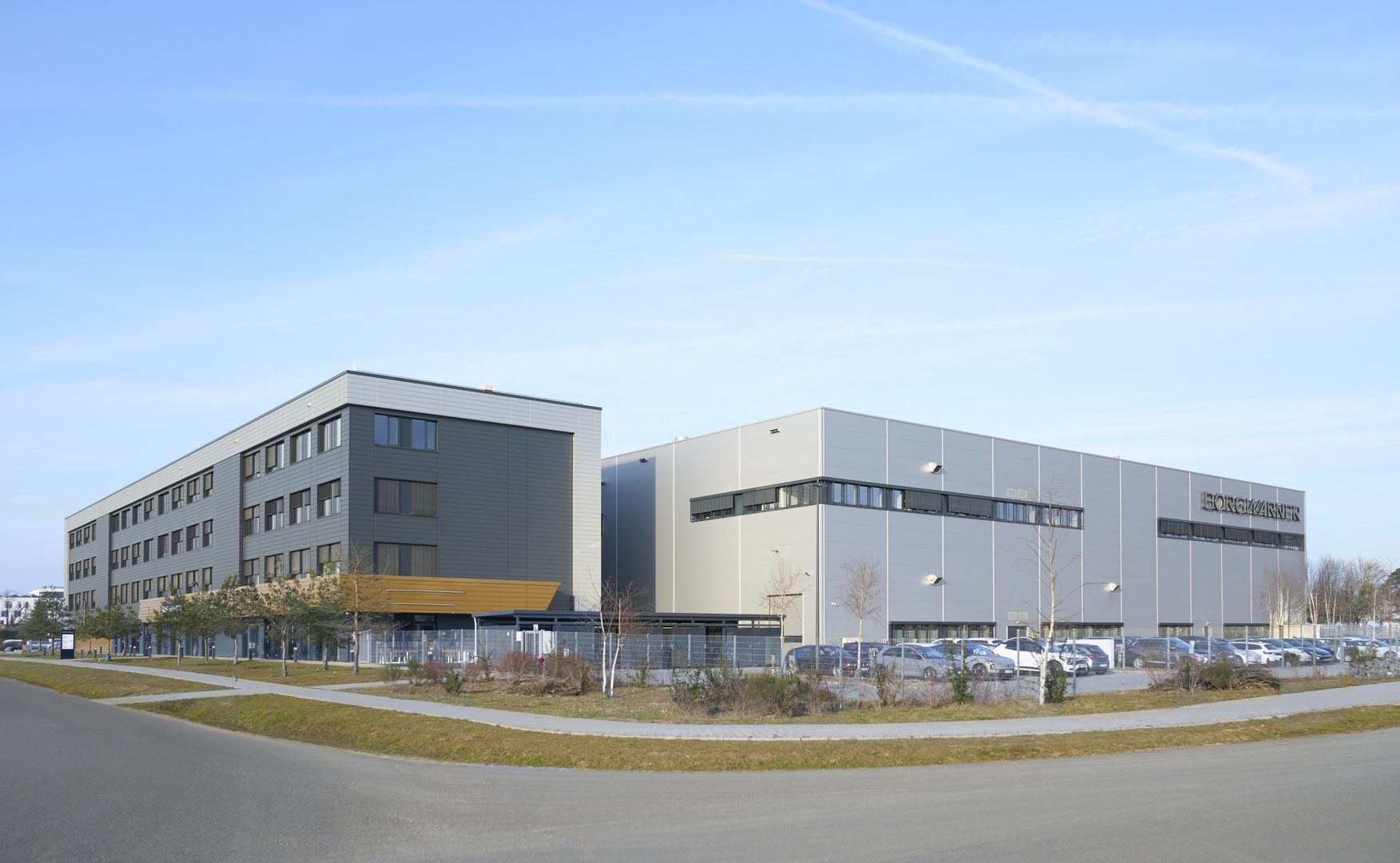
La Gigafactory di Darmstadt: qualche numero
A Darmstadt, non lontano da Francoforte, produzione, area testing, uffici e R&D occupano circa 15 mila metri quadrati, a cui si aggiungono i 4.000 metri quadrati del vicino sito di Langen. In totale sono più di 850 le persone impegnate nella progettazione e realizzazione di moduli e pacchi batterie, ma anche di Bms (sistemi per la gestione delle stesse) e Rcb (Removable contator box). In soldoni, dal 2022 solo in Germania la divisione battery systems BorgWarner ha prodotto circa 5 GWh di accumulatori per veicoli commerciali e industriali con tecnologia Nmc (nichel-manganese-cobalto), destinati ad aumentare notevolmente quando verrà raggiunta la capacità massima del sito di 3,5 GWh, anche grazie alla finalizzazione di una seconda linea produttiva altamente automatizzata. Considerando anche l’altro plant americano in South Carolina, nel 2025 il gruppo si aspetta una produzione di circa 5,4 GWh.
Gli ingegneri di BorgWarner ci hanno illustrato il funzionamento delle linee, che si articolano su due piani. Si comincia dall’inserimento delle celle cilindriche all’interno dei moduli: i pacchi batterie di terza generazione attualmente prodotti da BorgWarner ammettono due strati da 300 celle, per un totale di 600 celle a modulo. I processi di incollaggio (inclusa la preparazione della superficie della cella) e l’aggiunta delle connessioni elettroniche – entrambi affidati ai robot – costituiscono la parte più complessa. La produzione di un singolo modulo, che pesa circa 50 chili, richiede più di un’ora, con un intervallo di pochi minuti tra la produzione di un modulo e il successivo.
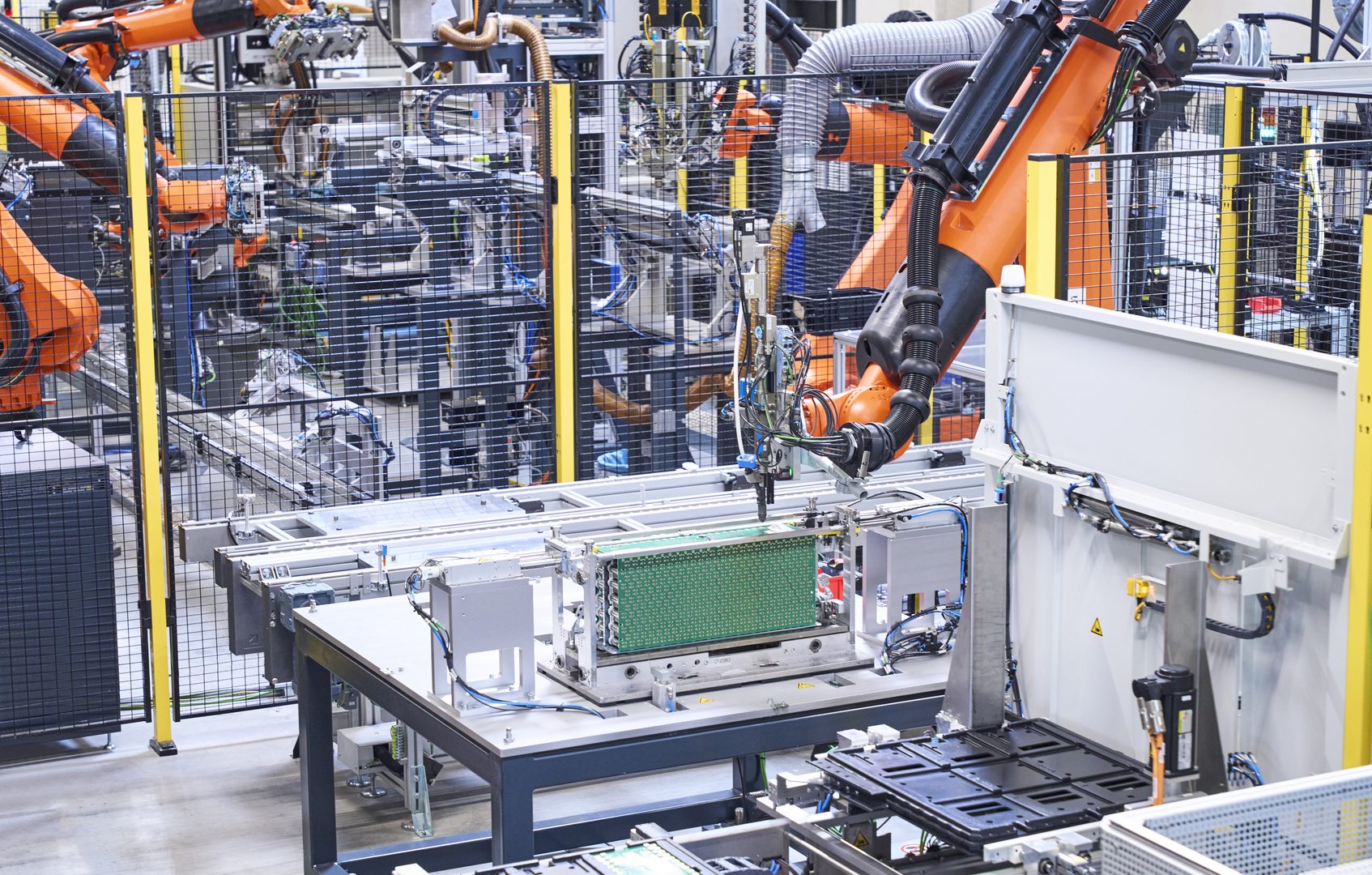
L’assemblaggio dei pacchi batterie
Il processo produttivo dei pacchi batterie, quindi l’inserimento dei moduli, è relativamente più semplice e anch’esso affidato ai robot industriali per questioni di affidabilità e gestione dei pesi. Sono ben poche, nel complesso, le attività manuali, principalmente di asservimento e gestione delle macchine. Ogni 20 minuti circa la linea realizza un pacco batterie da 9 moduli. Interessante e all’avanguardia anche l’area testing, adiacente alla produzione: poco più di 2.000 metri quadrati in cui vengono sottoposti a vari tipi di test (corrosione, immersione in acqua per monitorare la tenuta, temperatura, prestazioni, resistenza alle vibrazioni, tenuta alla carica) i pacchi batterie, ma anche le celle che, sebbene provenienti da fornitori esterni, sono sottoposte a verifiche rigorose in ambienti controllati.
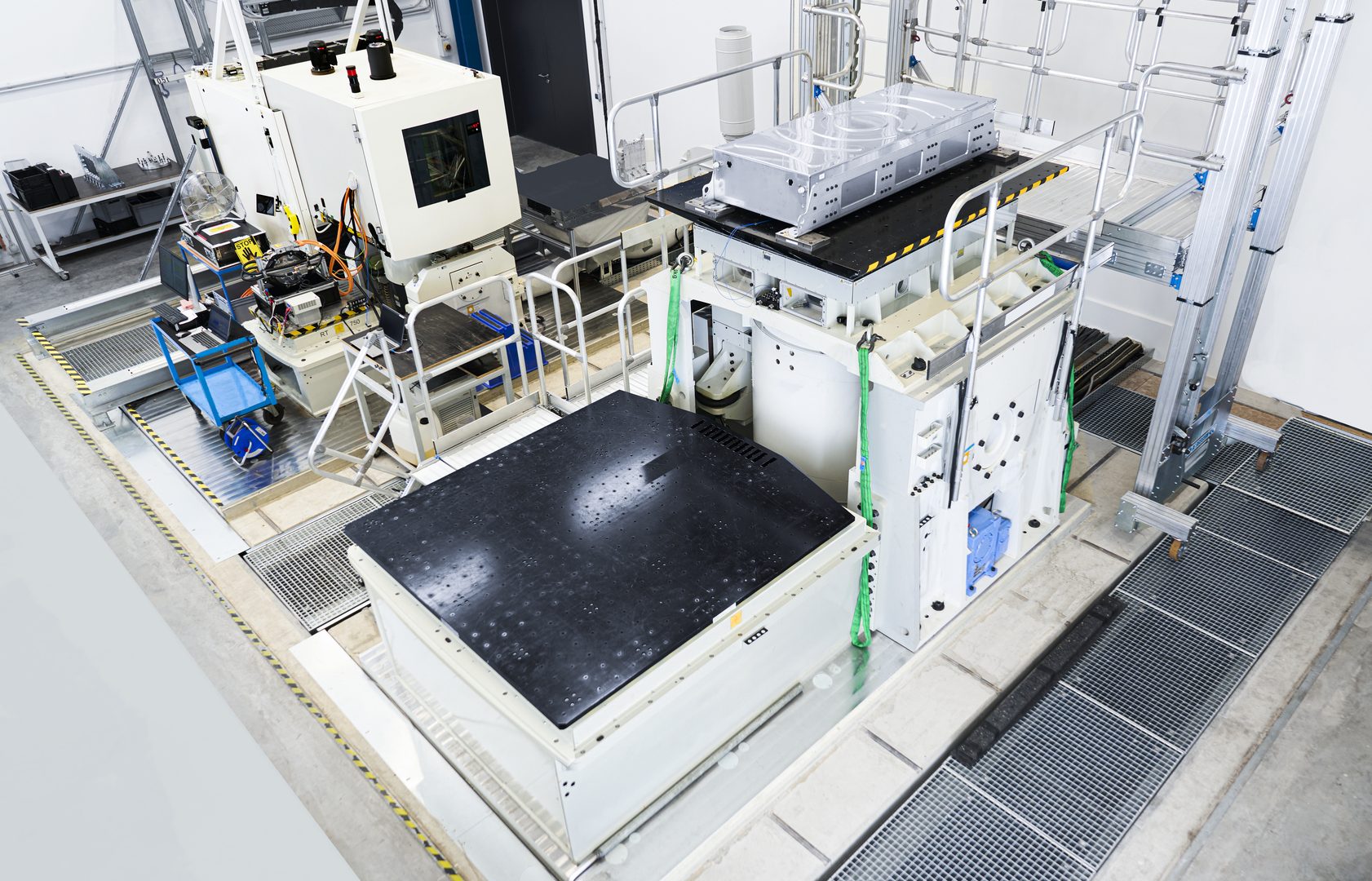
La terza generazione di pacchi batterie Uhe BorgWarner, quelli che escono attualmente dalle linee di Darmstadt, garantisce una capacità di 98 kWh con un voltaggio nominale di 665 V, potenza di ricarica in corrente continua fino a 80 kW e peso di poco inferiore ai 600 chili. Molto importante per il settore a cui sono destinati i pacchi batterie, quello dei veicoli commerciali e industriali, è la garanzia di funzionamento ottimale sui 4.000 cicli di ricarica, molto superiore rispetto alle batterie per auto. In portfolio anche la versione compatta con 5 o 6 moduli al posto dei 9 canonici. Camion, autobus, veicoli off-road (escavatori, battipista, piattaforme aeree) e applicazioni marine sono quelle d’elezione per gli accumulatori BorgWarner, a cui si aggiungono sperimentazioni nell’ambito degli eTrailer. Molto rilevante fino a questo momento il comparto dei bus: secondo il gruppo statunitense, un e-bus su 5 in Europa e negli States monta batterie BorgWarner.
In attesa che il mercato dei truck elettrici si consolidi
E i truck? Il mercato, lo sappiamo, non è florido e in BorgWarner ne sono consapevoli. Vogliono, però, farsi trovare pronti quando i numeri saranno più significativi. E stanno investendo in nuovi prodotti, a partire dalla tecnologia Lfp (litio-ferro-fosfato) per le celle: non rimpiazzeranno quelle Nmc prodotte oggi, ma saranno complementari e la scelta verrà fatta sulla base dell’applicazione. BorgWarner ha in programma una diversificazione dell’offerta in termini di forma e dimensione dei pacchi batterie, con l’evidente obiettivo di venire incontro alle esigenze costruttive degli Oem, bus e truck in testa (al momento, gli Lcv non sono nel radar di BorgWarner).
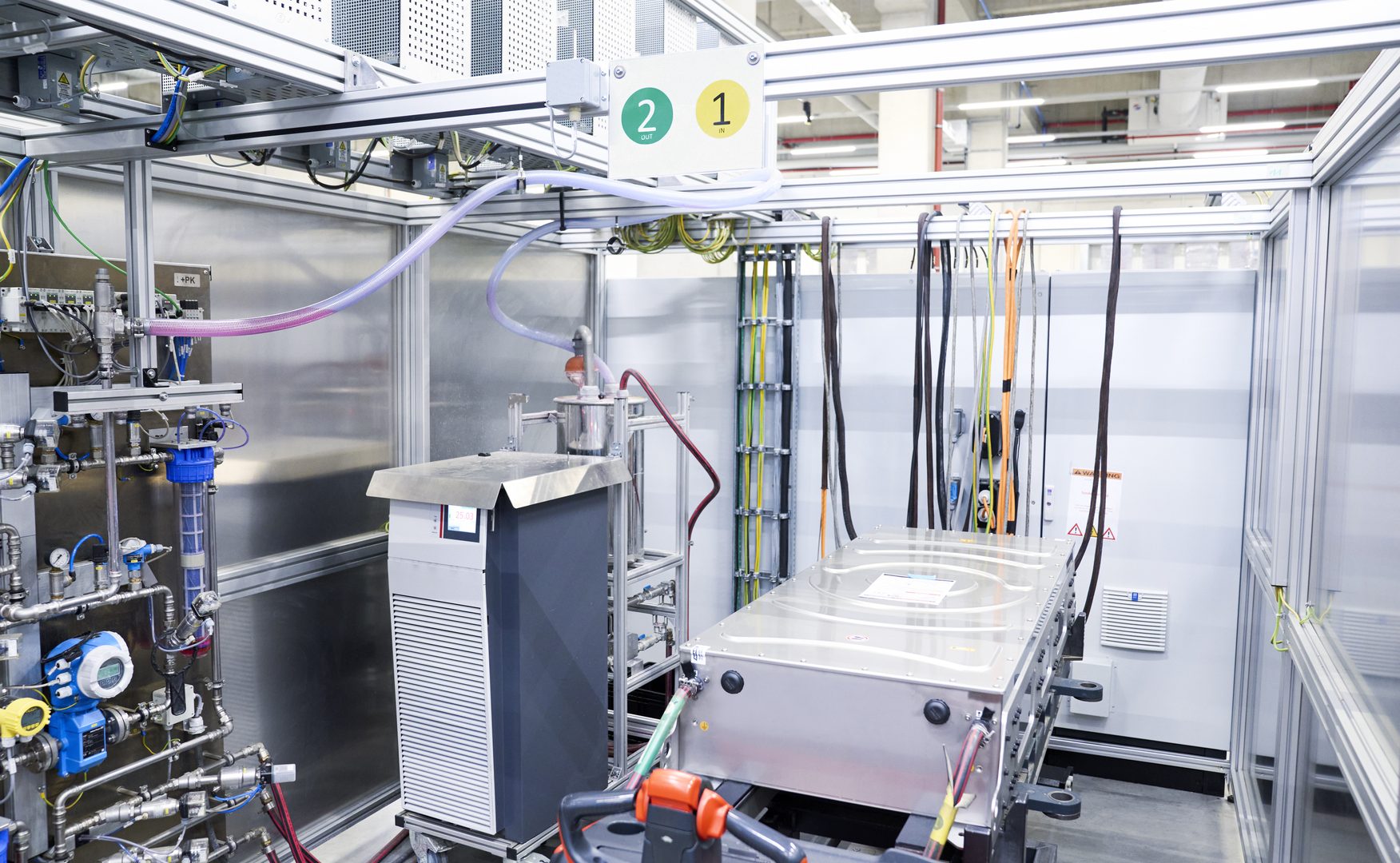
Guardando, appunto, allo sviluppo delle batterie Lfp, il portfolio sarà costituito da prodotti piatti (flat), alti, compatti o cubici, senza alterare le logiche hardware e software applicate finora (hardware e software foundation, si chiama questa filosofia). E non cambierà, almeno per i prossimi anni, la strategia di base di BorgWarner, che continuerà a rivolgersi a fornitori di fiducia – cinesi per le batterie Lfp, anche di altre nazioni per le Nmc – per quanto riguarda le celle. In questa direzione va evidentemente la partnership FinDreams Battery, siglata lo scorso anno per la fornitura in esclusiva (fuori dalla Cina) delle, queste sì, rivoluzionarie ‘blade cells’ che, grazie a un design innovativo e particolarmente compatto, garantirà ancora più flessibilità ai costruttori.
Un progetto ‘win-win’ su quale a Darmstadt mostrano di credere molto. I recenti scossoni che hanno investito la giovane industria europea delle batterie nelle scorse settimane danno senza dubbio valore alla scelta.